Maschinensicherheit – rechtliche Grundlagen und Risikoanalyse nach Maschinenrichtlinie 2006/42/EG
03.09.2019 | JS – Online-Redaktion, Forum Verlag Herkert GmbH
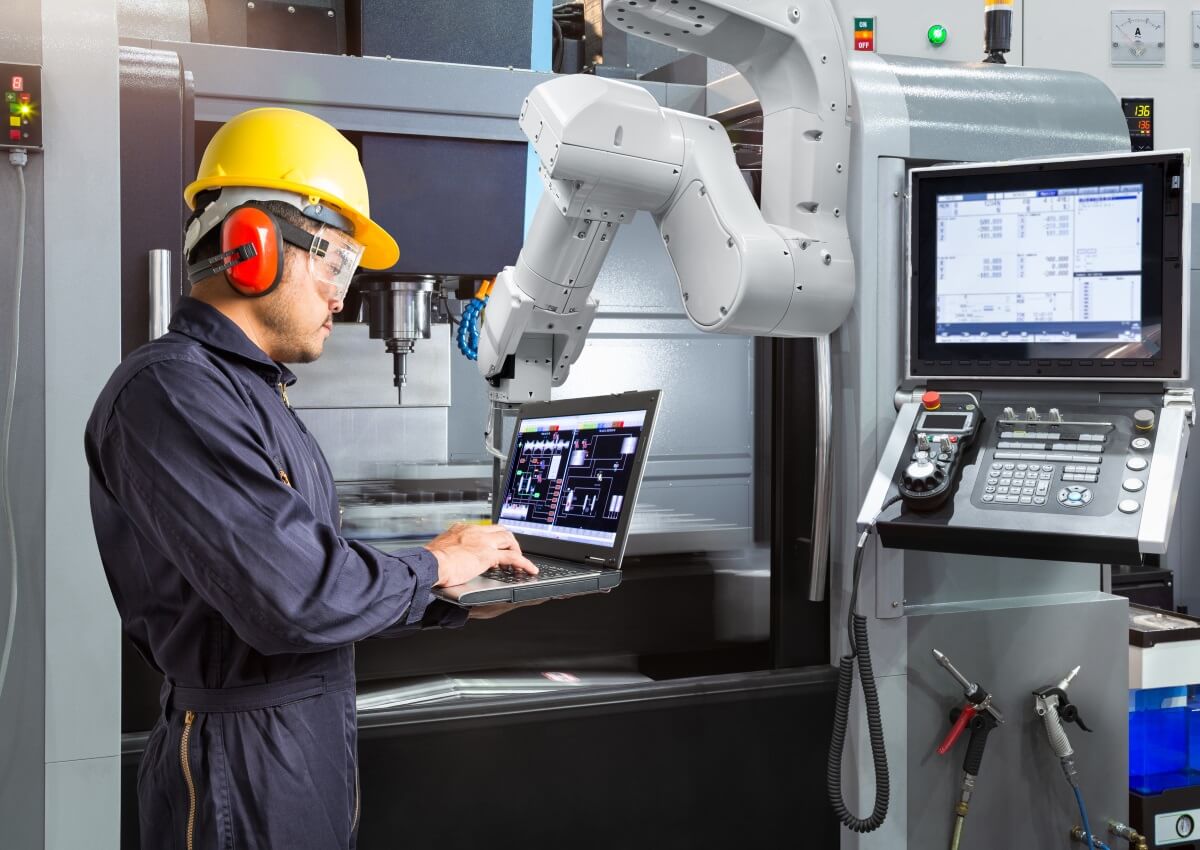
Rechtliche Grundlagen zur Maschinensicherheit
Hinsichtlich der Maschinensicherheit müssen Betreiber und Hersteller zahlreiche rechtliche Vorschriften beachten. Das sind insbesondere die Maschinenrichtlinie 2006/42/EG und die Betriebssicherheitsverordnung (BetrSichV). Während Maschinenbetreiber hauptsächlich den sicheren Betrieb einer Maschine verantworten, müssen Maschinenhersteller bei der Konstruktion der Anlage die Anforderungen der Maschinenrichtlinie erfüllen, um die Maschinensicherheit gewährleisten zu können.
Die Maschinenrichtlinie stellt das Basiswerk zur Herstellung sicherer Maschinen dar und gilt auf europäischer Ebene, also für alle in Europa hergestellten Maschinen. Ein wichtiger Aspekt der Maschinensicherheit in Europa ist also, dass alle bereitgestellten Maschinen den Kriterien der Maschinensicherheit zu folgen haben – das gilt sowohl für neue als auch gebrauchte Maschinen.
Auf nationaler Ebene wurde die Maschinenrichtlinie im Rahmen des Produktsicherheitsrechts als Verordnung zum Produktsicherheitsgesetz (ProdSG) umgesetzt. Konkret ist die neunte Verordnung zum Produktsicherheitsgesetz (Maschinenverordnung) (9. ProdSV) die maßgebliche Gesetzesgrundlage für Maschinenhersteller in Deutschland. In der 9. ProdSV wird in mehreren Paragrafen die Einhaltung der Maschinenrichtlinie gefordert.
Des Weiteren sind hinsichtlich der Maschinensicherheit zahlreiche Normen zu beachten, wie z. B. die DIN ISO 12100 „Sicherheit von Maschinen - Allgemeine Gestaltungsleitsätze - Risikobeurteilung und Risikominderung“, die ein dreistufiges Verfahren zum Erreichen der maximalen Maschinensicherheit beschreibt. Im Bereich der Maschinensicherheit werden Normen in folgenden Kategorien eingeteilt:
- A-Norm (Sicherheitsgrundnorm): Norm, die Grundbegriffe, Gestaltungsleitsätze und allgemeine Aspekte enthält und die für alle Maschinen, Geräte und Anlagen angewandt werden kann.
- B-Norm (Sicherheitsfachgrundnorm): Norm, die einen Sicherheitsaspekt oder eine Art von Schutzeinrichtung behandelt und die für eine Reihe verschiedener Maschinen, Geräte und Anlagen verwendet werden kann:
- Typ B1-Norm behandelt bestimmte Sicherheitsaspekte (z. B. Sicherheitsabstände, Oberflächentemperatur, Geräusch).
- Typ B2-Norm behandelt Schutzeinrichtungen (z. B. Zweihandschaltungen, Verriegelungen, Kontaktmatten, trennende Schutzeinrichtungen)
- C-Norm (Maschinensicherheitsnorm): Norm, die detaillierte Sicherheitsanforderungen für eine bestimmte Maschine oder Gruppe von Maschinen behandelt.
C-Normen haben grundsätzlich Anwendungsvorrang gegenüber von B- und A-Normen.
Alle gesetzlichen und normativen Vorgaben zur Maschinensicherheit erhalten Hersteller und Betreiber mit dem „Praxisratgeber Maschinensicherheit“. Das Werk beinhaltet zudem fallbezogene Handlungsanleitungen und praktische Arbeitshilfen zum Download.
Risikoanalyse nach Maschinenrichtlinie 2006/42/EG
Für das Inverkehrbringen neuer Maschinen in Europa schreibt die Maschinenrichtlinie eine CE-Kennzeichnung verbindlich vor. Diese kann der Hersteller allerdings erst dann an der Maschine anbringen, wenn er nachweisen kann, dass seine Maschine alle Anforderungen der Maschinenrichtlinie 2006/42/EG erfüllt und Maschinensicherheit gegeben ist. Wichtiger Aspekt auf dem Weg dahin ist die Risikoanalyse, die drei Prozessphasen vereint:
- Risikobeurteilung
- Risikominderung
- Nachweis
Risikobeurteilung
Bei der Beurteilung der Risiken, die von Maschinen für den Menschen ausgehen, werden alle vorhersehbaren Gefährdungen analysiert – und zwar in allen Lebensphasen der Maschine (Errichtung, Betrieb, Wartung etc.). Anschließend wird das Risiko bewertet und in Relation gesetzt. Bei vielen (Produktions-)Maschinen kann eine Gefährdung oft nicht ganz ausgeschlossen werden, ohne ihre Funktionalität zu beeinträchtigen.
Das Ziel der Risikobeurteilung ist deshalb nicht, sämtliche Gefährdungen auszuschließen, sondern diese auf ein akzeptables Niveau zu bringen. Die Aufgabe ist also, einen Kompromiss zwischen der Funktion und Aufgabe der Maschine und einer ausreichenden Maschinensicherheit herzustellen.
Risikominderung
Die Minderung auf ein akzeptables Restrisiko erfolgt nach einer 3-Stufigen-Methode gemäß ISO 12100:
- Zuerst wird geprüft, ob das angestrebte Sicherheitsniveau durch eine sichere Konstruktion hergestellt werden kann.
- Ist das Restrisiko nach Erfüllung des ersten Punkts noch zu hoch, werden zusätzlich technische Maßnahmen ergriffen.
- Auch wenn die ersten Maßnahmen zum gewünschten Ergebnis führen, empfiehlt es sich, ergänzend anhand von Benutzerinformationen, die an der Maschine befestigt werden, auf Restrisiken hinzuweisen.
Danach wird abhängig vom Ursprungsrisiko eine Sicherheitsstufe hinsichtlich der Maschinensicherheit ermittelt. Hierfür greifen Maschinenhersteller auf zwei Normen zurück:
- ISO 13849-1 „Sicherheit von Maschinen - Sicherheitsbezogene Teile von Steuerungen - Teil 1: Allgemeine Gestaltungsleitsätze“
- IEC 62061 „Sicherheit von Maschinen - Funktionale Sicherheit sicherheitsbezogener elektrischer, elektronischer und programmierbarer elektronischer Steuerungssysteme“
Anschließend werden die benötigten Sicherheitskomponenten ausgewählt und mit einem Tool überprüft, ob die Sicherheitsstufe erreicht werden kann, womit die Anforderungen aus der Risikobeurteilung als erfüllt gelten.
Nachweis
Um den Nachweis über die Maschinensicherheit zu erbringen, werden alle Maßnahmen überprüft und dokumentiert. Nach einer erfolgreichen Validierung stellt der Hersteller eine Konformitätserklärung gemäß Maschinenrichtlinie aus und bringt diese neben dem CE-Kennzeichen an der Maschine an.
DIN EN 60204-1 zur Prüfung elektrischer Ausrüstung von Maschinen wurde 2019 novelliert
Eine CE-Kennzeichnung von Maschinen ohne Anwendung der DIN EN 60204-1 (VDE 0113-1:2019-06) „Sicherheit von Maschinen – Elektrische Ausrüstung von Maschinen“ ist in der Praxis gar nicht möglich. Denn so gut wie jede Maschine hat inzwischen elektronische Bestandteile und Teil 1 der DIN EN 60204 gilt für elektrische, elektrotechnische und programmierbare elektronische Ausrüstungen und Systeme von Maschinen. Sie gehört also zu den Normen hinsichtlich der Maschinensicherheit, die Hersteller, Anlagenbauer und Betreiber von Maschinen zwingend beachten müssen.
Die DIN EN 60204-1 ist im Juni 2019 in novellierter Fassung erschienen und vertieft die grundlegenden Anforderungen an die elektrische Ausrüstung von Maschinen. Auch, wenn die Neufassung keine besonderen oder zusätzlichen Anforderungen festlegt, gibt es u. a. folgende Neuerungen:
- Der Bemessungsstrom der gesamten elektrischen Ausrüstung muss nun ermittelt und angegeben werden. Ausgenommen von dieser Regelung sind Stromkreise von Schaltgerätekombinationen.
- Neu in die DIN EN 60204-1 aufgenommen wurden „Einrichtungen zum Trennen und Ausschalten“.
- Die Neufassung der DIN EN 60204-1 enthält nun auch das Thema Erdschluss-/Fehlerstromschutz. Neu ist, dass Fehlerstromschutzeinrichtungen (RCD) nun generell gefordert werden, und zwar mit einem Bemessungsdifferenzstrom von IΔn ≤ 30 mA.
- Die neue DIN EN 60204-1 greift nun auch die sichere Einbindung von Frequenzumrichtern auf. Ganz neu sind die Vorgaben zur Prüfung von Power-Drive-Systemen.
- Hinsichtlich der Dokumentation werden nun neben der Angabe des Bemessungskurzschlussstroms auch die Durchführung einer Wärmeberechnung sowie die Erstellung einer Wärmebilanz gefordert.
- Ebenfalls neu ist, dass die Dokumentation von EMV-Störfestigkeits- und Emissionstests verpflichtend wird.
Hinweis: Selbst wenn die DIN EN 60204-1 das ausschlaggebende Regelwerk zur Prüfung der elektrischen Ausrüstung von Maschinen ist, kommen Prüfer nicht umhin, auch auf andere normative Vorgaben zurückzugreifen. Warum und welche das sind, zeigt der Beitrag „Prüfung von Maschinen nach DIN EN 60204-1 (VDE 0113-1) – warum Prüfer auch auf andere Regelwerke zurückgreifen müssen“.
Produktempfehlung
Bei der Durchführung der Prüfung unterstützt das aktualisierte „Handbuch Prüfung elektrischer Maschinen“ mit Schritt-für-Schritt-Anleitungen und einsatzfertigen Arbeitshilfen zum Herunterladen.
Quellen: „Praxisratgeber Maschinensicherheit“, „Elektropraktiker“